Wbrew powszechnemu przekonaniu o „nowoczesności” tego typu obiektów, pierwsza na świecie przemysłowa spalarnia odpadów powstała już w 1874 roku w brytyjskim Nottingham. W Polsce od 2001 roku nie uruchomiono dotąd nowej instalacji termicznego przekształcania odpadów komunalnych, choć przyjęta przez Unię Europejską strategia gospodarki odpadami oraz dyrektywa dotycząca ich składowania z 1999 roku ogranicza dozwoloną ilość odpadów niepodlegających przetworzeniu do 65% (w stosunku do danych z 1995 roku). Najlepszym sposobem na ich zagospodarowanie jest przekształcenie w energię poprzez spalenie. Za budową nowoczesnych spalarni przemawia więc dodatkowo fakt ograniczenia zużycia paliw kopalnych oraz zmniejszenia emisji CO2 przez spalanie biomasy. W Europie działa już ponad 450 spalarni, a w najbardziej rozwiniętych krajach Unii udział spalania odpadów wynosi 30%-50%, przy jednoczesnej śladowej ilości śmieci składowanych na wysypiskach (1%-5%). W Polsce te proporcje są niemal odwrotne, bowiem aż 75% trafia na składowiska, 13% podlega recyklingowi, 12% kompostowaniu, a jedynie 0,5% spaleniu. W ciągu najbliższych 5 lat stan ten powinien ulec zmianie. Do jedynej funkcjonującej obecnie w Polsce spalarni odpadów komunalnych w Warszawie dołączą kolejne. Do końca 2015 roku powinno zostać oddanych w sumie sześć spalarni, których wydajność wyniesie ok. 1 mln Mg/rok (1 mln ton/rok). Aby jednak ograniczyć ilość składowanych odpadów do poziomu określonego w Dyrektywie Unijnej, do 2020 roku należałoby zbudować jeszcze 10-15 tego typu obiektów.
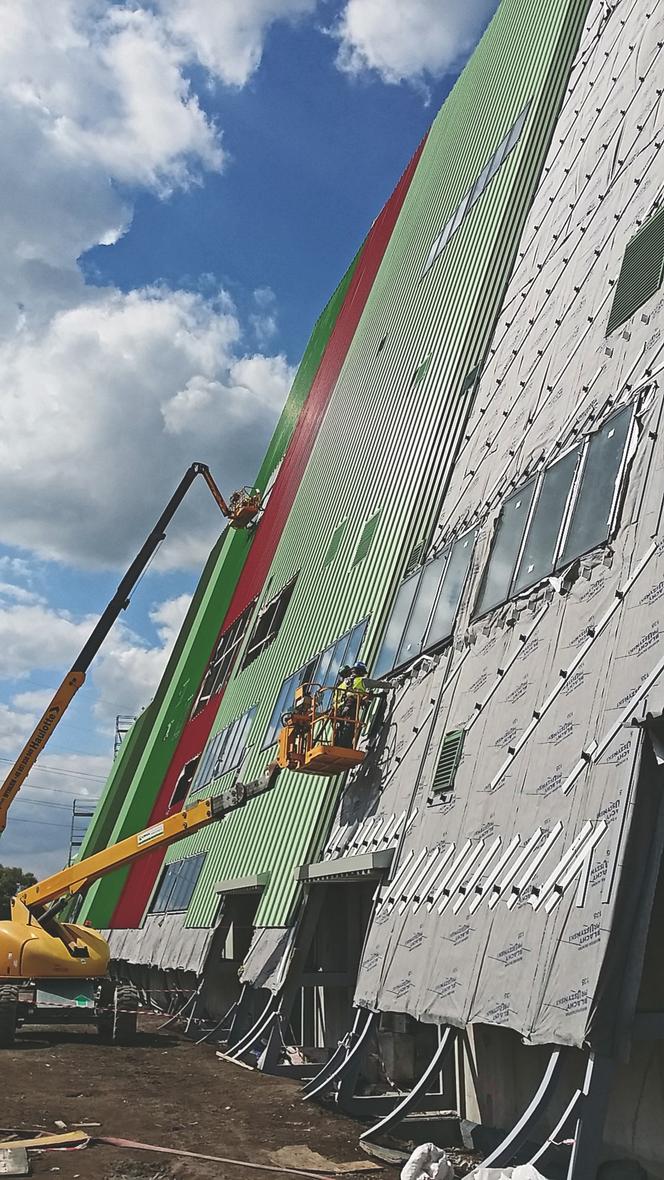
i
Największym z sześciu obecnie budowanych jest Zakład Termicznego Przekształcania Odpadów w Krakowie (ZTPO). Do spalenia będą tam przeznaczone odpady, których nie da się odzyskać poprzez segregację i kompostowanie. Krakowski zakład wykorzystując je jako paliwo, będzie dodatkowo produkował energię elektryczną i cieplną na potrzeby miasta. Inwestorem przedsięwzięcia jest Krakowski Holding Komunalny S.A., a realizacja finansowana jest z kilku źródeł: z Unii Europejskiej (w ramach Funduszu Spójności), wkładu własnego KHK oraz pożyczki zaciągniętej przez holding w Narodowym Funduszu Ochrony Środowiska i Gospodarki Wodnej. Szacowany koszt realizacji wynosi ok. 826 mln zł brutto.
HistoriaProjekt budynku został wybrany w konkursie z 2010 roku. Zwyciężyła koncepcja zespołu: Bogusław Wowrzeczka (Manufaktura nr 1), Michał Teller (Teller Architekci) oraz Filip Łapiński (Łapiński Architekci). Na podstawie tego projektu Przedsiębiorstwo PROCHEM S.A. przygotowało projekt budowlany i wykonawczy, w którym uczestniczyły również firmy Manufaktura nr 1 Bogusław Wowrzeczka, Teller Architekci i Łapiński Architekci. Pracami projektowymi ze strony PROCHEM-u kierował architekt Jakub Baczyński. W koncepcji konkursowej kompozycja obiektu inspirowana była między innymi liniowym układem pól uprawnych. Forma architektoniczna, jako płynnie wypiętrzająca się z terenu wielobarwna wstęga, miała sprawiać wrażenie harmonijnego zespolenia z otaczającym naturalnym krajobrazem. W projekcie budowlanym i wykonawczym udało się zachować generalną dyspozycję przestrzenną zespołu, jednak z pewnymi zmianami podyktowanymi względami technologicznymi i redukcją kosztów budowy. Wpłynęło to na pewne uproszczenie formy. Ze względu na koszty i wymagania pielęgnacyjne zrezygnowano także z koncepcji „opakowania” dachów i ścian obiektu wielobarwną roślinnością, która była jednym z ważnych elementów projektu konkursowego. Pozwolenie na budowę uzyskano jesienią 2013 roku. W tym samym roku generalny wykonawca inwestycji, południowokoreańska firma Posco E&C, rozpoczął realizację. Jej zakończenie planowane jest na koniec 2015 roku.
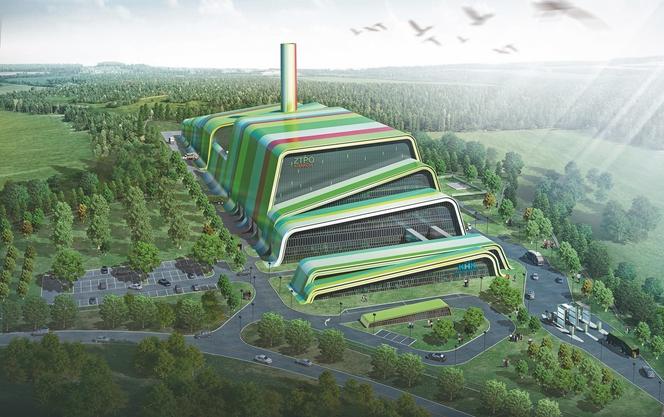
i
Parametry inwestycji i lokalizacjaDocelowa wydajność ZTPO wyniesie ok. 220 tys. ton rocznie (obecnie każdy mieszkaniec Krakowa produkuje 300 kg śmieci w ciągu roku, co daje 327 tys. ton). Dla zakładu zaprojektowano dwie linie technologiczne do termicznego przekształcania odpadów komunalnych. Nominalna wydajność każdej z nich wynosić będzie 14,1 Mg/h. Zakład będzie ponadto produkować ok. 65 tys. MWh energii elektrycznej i ok. 280 tys. MWh energii cieplnej dla miasta. W tym celu wybudowano 3,5-kilometrową nitkę rurociągu ciepłowniczego oraz linię energetyczną 110 kV o długości 250 m służącą do przesyłu energii wytwarzanej w zakładzie. Krakowska spalarnia została zlokalizowana na miejskiej działce położonej przy ul. Giedroycia w Dzielnicy XVIII Nowa Huta. Był to niezagospodarowany teren, położony w sąsiedztwie czynnego składowiska popiołów i żużli Elektrociepłowni Kraków, pozbawiony elementów podlegających ochronie pod względem przyrodniczym. Realizowany obecnie układ przestrzenny ZTPO stanowi połączony łącznikami i pomostami technologicznymi zespół obiektów mieszczących kolejno: budynek administracyjno- socjalno-edukacyjny, budynek procesowy i budynek gospodarki pozostałościami procesowymi. Całość uzupełniają dwie wiaty: osłaniająca kontenery stacji transformatorowej oraz parkingowa. Bryła główna, przy szerokości dochodzącej do 80 m, rozciąga się na długości 300 m i sięga niemal 40 m wysokości. Powierzchnia zabudowy obiektów wynosi 18,5 tys. m2, powierzchnia netto około 30 tys. m2, a kubatura całości niemal 400 tys. m3. Obsługę komunikacyjną poprowadzono po obwodzie pasma zabudowy, przewidując dwa wjazdy od strony ul. Giedroycia – zachodni dla samochodów ciężarowych i północno-zachodni dla osobowych.
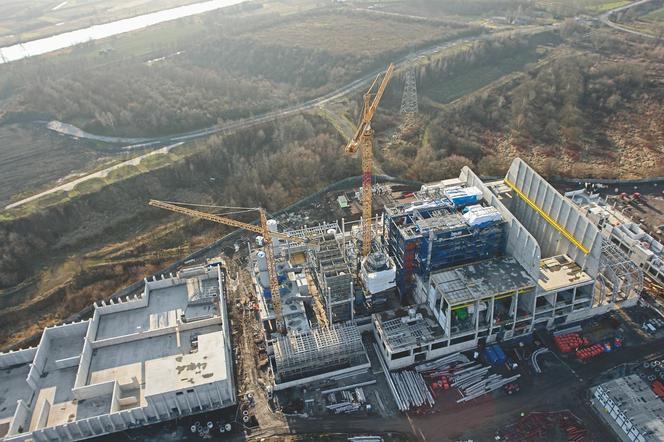
i
Proces technologicznyTermiczne przekształcanie odpadów przebiegać będzie w głównym budynku procesowym z wykorzystaniem technologii pieców z rusztem do spalania. Zastosowane instalacje spełniają kryteria BAT (Best Available Techniques), a technologie były sprawdzone poprzez wieloletnie i liczne doświadczenia. W budynku procesowym ulokowano współpracujące ze sobą następujące strefy: węzeł przyjmowania i przygotowania odpadów, węzeł spalania i odzyskiwania energii, węzeł wytwarzania i przesyłania energii elektrycznej i węzeł oczyszczania spalin. W budynku podprocesowym przewidziano zaś węzeł waloryzacji żużla oraz stabilizowania i zestalania popiołów. Za głównym wjazdem do zakładu powstanie stanowisko ważenia ciężarówek oraz kontroli na obecność substancji radioaktywnych. Rozładunek następować będzie do jednokomorowego bunkra w hali rozładunku. Szacunkowo zakład będzie mógł obsłużyć 150 samochodów dziennie. Transportem suwnicowym i chwytakami odpady będą podnoszone z bunkra i podawane do lejów zasypowych, skąd podajnikiem dostaną się do komór spalania dwóch pieców rusztowych. Odzysk ciepła ze spalin będzie następował w procesie podgrzewania nimi wody przepływającej przez tzw. kocioł odzysknicowy. Para wytwarzana w wymiennikach dostarczana będzie do turbozespołu, gdzie zamieni się w energię elektryczną, oraz do miejskiej sieci ciepłowniczej. Gazy odlotowe powstające w procesie spalania mają być oczyszczane stopniowo: najpierw w komorze dopalania, następnie w absorberze metodą półsuchą, a na końcu w filtrach workowych.Oczyszczone spaliny przy pomocy głównego wentylatora ciągu wyprowadzane zostaną do atmosfery kominem o wysokości 70 m. Popiół i żużel wytworzony w piecach rusztowych zostanie schłodzony do temperatury poniżej 90°C i przesłany do węzła waloryzacji żużla za pomocą szczelnych przenośników taśmowych między głównym budynkiem procesowym a budynkiem gospodarki pozostałościami procesowymi. Po waloryzacji żużel poddawany będzie badaniom laboratoryjnym, w celu określenia możliwości dalszego wykorzystania w budownictwie.
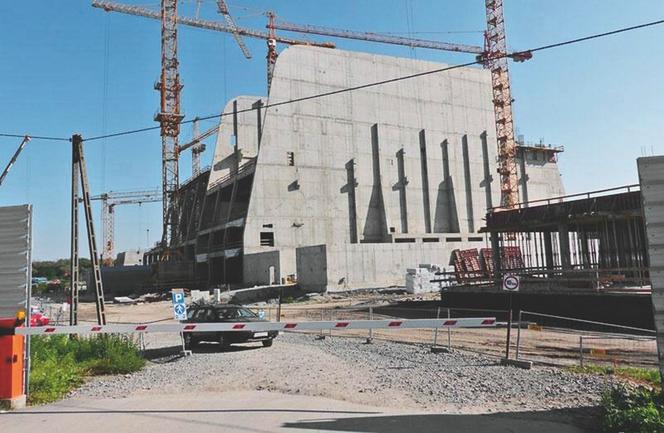
i
Forma obudowyBiorąc pod uwagę zautomatyzowany i odporny na czynniki atmosferyczne charakter procesu technologicznego, mógłby on funkcjonować równie dobrze bez obudowy. Realizowana obudowa technologii ma jednak w tym wypadku pełnić dwie funkcje. Pierwsza to stworzenie jednolitej, przyjaznej dla otoczenia formy obiektu, druga – zapewnienie optymalnych warunków pracy dla obsługi i konserwacji urządzeń technologicznych. Forma obudowy płynnie „wychodzi” z poziomu terenu, by następnie przejść nachylonymi pod różnymi kątami (65-85 stopni) ścianami w płaszczyzny dachu, oplatając w ten sposób budynek. Jak już wspomniano, celem takiego założenia projektowego było uzyskanie formy organicznie powiązanej z krajobrazem. W znaczącym stopniu zewnętrzna obudowa odzwierciedla również wewnętrzne zróżnicowanie gabarytów urządzeń technologicznych. Każdy z budynków w paśmie składa się ze różnych wysokościowo segmentów – kolorowych wstęg – wyodrębnionych poprzecznie w stosunku do podłużnej osi zakładu. Segmenty z początku niskie, o wysokości 10 m, stają się coraz wyższe w miarę zbliżania się do środka zespołu, gdzie osiągają 40 m (hala kotłów), aby następnie obniżyć się do 14 m. Dominantą założenia jest 70-metrowy komin.
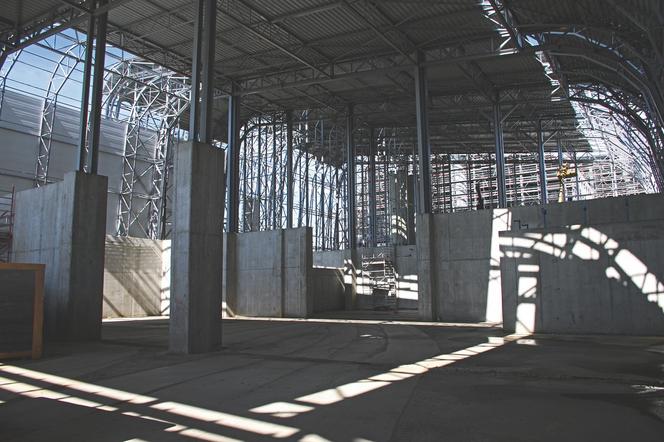
i
Budowa – konstrukcja i materiałZ uwagi na skomplikowane warunki geotechniczne oraz wysoki poziom wód gruntowych, fundamenty budynku procesowego zostały wykonane jako żelbetowe w technologii ścian szczelinowych o grubości 600 i 800 mm oraz płyty fundamentowej o zróżnicowanej grubości – od 60 do 250 cm. Tę ostatnią posadowiono na palach CFA Ø600 o długości od 6 do 15 m i sięgających do 18 m poniżej poziomu terenu. Również fundamenty budynku gospodarki pozostałościami procesowymi wykonano jako żelbetowe, na palach SDP Ø400 o długości ok. 8 m. Obiekt biurowy w części parterowej posadowiono na palach, a część podziemną zaprojektowano w technologii żelbetowej z betonu wodoszczelnego. Konstrukcja budynku procesowego jest mieszana: żelbetowa i stalowa. Część podziemna oraz wielokondygnacyjna część administracyjna, główne stropy i słupy oraz oddzielenia pożarowe, zrealizowano w konstrukcji żelbetowej płytowo-słupowej z betonu zbrojonego, wylewanego na mokro. Stropy są monolityczne, żelbetowe, dwukierunkowo zbrojone, oparte na monolitycznych belkach i słupach. Całość konstrukcji żelbetowej wykonana została w postaci sztywnych ram ułożonych w dwóch kierunkach. Usztywnienie budynku zapewniają także ściany bunkra, ściany żelbetowe klatek schodowych i ściany przeciwpożarowe. Bunkier na odpady to żelbetowa szczelna wanna z płytą fundamentową na poziomie 9 m poniżej terenu. Nad bunkrem znajdują się dwie suwnice o nośności 85 t, oparte na żelbetowych słupach połączonych ścianami żelbetowymi. Kolejna suwnica, o nośności 40 t, znajduje się nad turbogeneratorem. Po wykonaniu konstrukcji żelbetowej, a przed zamknięciem obudową zewnętrzną, zrealizowano główne prace montażowe technologii dwóch linii kotłów wraz z konstrukcją wsporczą i pomostami komunikacyjnymi. W zakresie węzła przetworzenia i wyprowadzenia energii zamontowano turbinę i generator oraz wymienniki ciepłownicze. Konstrukcja stalowa obudowy budynku procesowego i podprocesowego obejmuje dach wraz ze słupami podpierającymi. Słupy stalowe wspornikowe oparte zostały na słupach żelbetowych. Dźwigary dachowe wraz ze skośnymi i pionowymi słupami stalowymi tworzą poprzeczne ramy, stężone w płaszczyźnie dachu co 10 m.
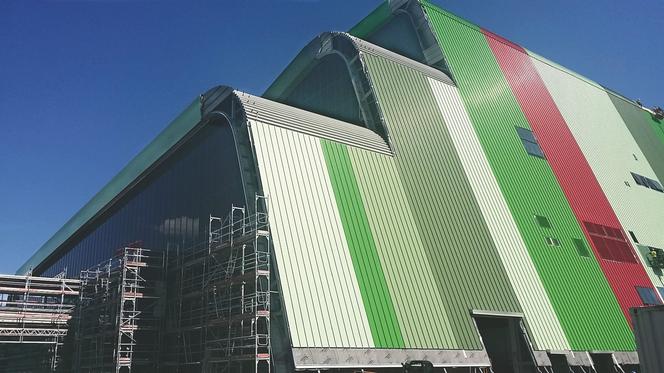
i
Ściany szczytowe stężone zostały w przęsłach skrajnych. Równolegle do montażu konstrukcji pod zewnętrzną obudowę prowadzono skomplikowane roboty w zakresie rozmieszczenia systemów technologicznych towarzyszących, tj. oczyszczania spalin, sprężonego powietrza, przygotowania wody procesowej i instalacji oczyszczania ścieków oraz pompowni technologicznych. Z uwagi na położenie zakładu na terenie potencjalnie zagrożonym powodzią, główne obiekty technologiczne musiały zostać odpowiednio zabezpieczone, aby nie dopuścić do skażenia środowiska. W tym celu zaprojektowano na obwodzie budynków szczelne ściany żelbetowe o wysokości 4 m. Wjazdy i wejścia do obiektów technologicznych zostały wyposażone w specjalne wodoszczelne wrota, które w przypadku powodzi automatycznie zamykają wszystkie otwory zewnętrzne. Wrota zamontowano od strony wewnętrznej, aby nie zakłócać formy obudowy. Najbardziej charakterystycznym elementem spalarni jest jej wielobarwna obudowa z blachy aluminiowej. Nachylona pod różnymi kątami powłoka każdego budynku zaprojektowana została z podłużnych arkuszy blachy aluminiowej, łączonych w technologii rąbka stojącego. Blacha stanowi zewnętrzną warstwę ścian z nośną warstwą z kaset stalowych wypełnianych wełną mineralną, mocowanych do słupów w rozstawie co 6 m. Na górnych łukach i dachu rolę warstwy nośnej przejmuje natomiast blacha trapezowa. Z uwagi na bardzo długie arkusze, dochodzące do 36 m, ich transport, a następnie montaż stanowił duże wyzwanie dla wykonawcy. Długość arkuszy była podyktowana koniecznością zredukowania liczby dylatacji w celu uzyskania jak najdłuższych, ciągłych płaszczyzn elewacji. Z tego powodu koryta i wpusty dachowe, a także urządzenia wentylacyjne rozmieszczono w sposób pozwalający na zamontowanie arkuszy bez konieczności naruszania ich ciągłości. Ściany pionowe, przeszklone, wykonano jako systemowe, kurtynowe słupowo-ryglowe, z profili aluminiowych w kolorze szarym, z wypełnieniem kwater szkłem przeziernym i nieprzeziernym. Konstrukcja ścian mocowana jest do stalowych belek rozpiętych między słupami.
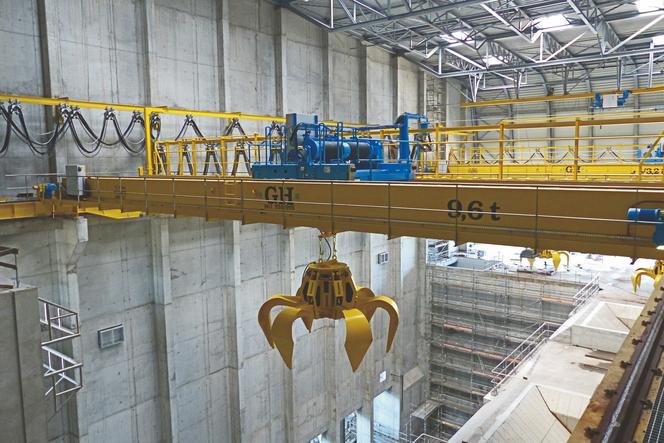
i
Ścieżka edukacyjnaBudowa spalarni odpadów jest powodem licznych protestów organizacji ekologicznych. Ich przedstawiciele uporczywie twierdzą, że jest ona szkodliwa dla ludzi i środowiska, choć badania dowodzą, że współczesne obiekty tego typu są całkowicie bezpieczne dla otoczenia. Odpowiedzią na stawiane zarzuty jest szeroko zakrojona akcja edukacyjna, której celem jest budowanie świadomości i wiedzy społeczeństwa na temat funkcjonowania termicznych spalarni śmieci. W tym celu, podobnie jak w większości spalarni w Europie, na terenie ZTPO zaprojektowano ścieżkę edukacyjną. Zaczyna się ona się w budynku administracyjno-socjalno- edukacyjnym, gdzie znajduje się część ekspozycyjna oraz sala konferencyjna. Stąd do budynku procesowego goście przechodzić będą łącznikiem na poziomie pierwszego piętra. Pomost-galeria dla zwiedzających prowadzić będzie przez halę rozładunkową, a następnie wzdłuż laboratorium i centralnej dyspozytorni do budynku głównego. Odwiedzjący będą mieli możliwość wglądu we wnętrze bunkra zasypowego przez szklaną witrynę kabiny operatora suwnicy. Ścieżka prowadzi przez najważniejsze strefy technologiczne przekształcania odpadów, a także do budynku gospodarki pozostałościami procesowymi. W programie zaplanowano również spacery po terenie zakładu.

i
Forma, technologia i ekologiaParafrazując znaną maksymę Louisa Sullivana form follows function, można powiedzieć, że w przypadku architektury krakowskiej spalarni form follows technology. W istocie, realne potrzeby technologiczne miały znaczący wpływ na ostateczny kształt zakładu. Z uwagi na przyjęte do realizacji gabaryty kotłów i towarzyszącej im technologii, główny budynek procesowy, a wraz z nim biurowiec i budynek waloryzacji żużla musiały ulec poszerzeniu o 20 m w stosunku do pierwotnej koncepcji. Innym projektowym problemem było zmieszczenie dwóch kotłów wraz z pomostami obsługowymi pod dachem głównego budynku procesowego, którego wysokość ograniczała do 40 m decyzja o warunkach zabudowy. Wymagało to rezygnacji z kratownic stalowych nad halą kotłów na rzecz niższych dźwigarów blachownicowych o rozpiętości wynoszącej 40 m. Kontynuując wątek wpływu różnych czynników na formę, prawdziwe będzie również w tym wypadku twierdzenie form follows ecology, bowiem ideowo forma obiektu wpisuje się w otaczający krajobraz, a zastosowana w zakładzie najnowsza technologia minimalizuje skutki oddziaływania na środowisko. Wydaje się, że miała tutaj miejsce rzadko występująca w pracy architekta synergia formy, technologii i ekologii, co nie jest bez znaczenia dla uzyskania społecznej akceptacji dla realizacji tego typu inwestycji w przyszłości.
Autorzy tekstu:Bogusław Wowrzeczka (WA PWr, 1977), od 2002 roku prowadzi pracownię Manufaktura Nr 1. Autor m.in. budynku Zintegrowanego Centrum Dydaktycznego PWr.Michał Teller (WA PWr, 2005), laureat stypendium fundacji Alfreda Toepfera. Założyciel pracowni Teller Architekci. Autor m.in. projektu rozbudowy Opery Wrocławskiej (I nagroda).Jakub Baczyński (WBAiIŚ PŁ, 2003), architekt w firmie PROCHEM S.A.. Współautor m.in. Drugiego Zakładu NGK Ceramics Polska w Gliwicach.Filip Łapiński (WA PWr, 2005), od 2011 roku prowadzi pracownię Łapiński Architekci specjalizującą się w budownictwie mieszkaniowym oraz przemysłowym.