Koncepcja
Prace projektowe związane z realizacją Q22 sięgają roku 2009, kiedy to firma Echo Investment podjęła decyzję o budowie nowoczesnego wysokościowca przy skrzyżowaniu ulic Grzybowskiej i Jana Pawła II w ścisłym centrum Warszawy. Budynek zaplanowano w miejscu istniejącego od 1993 roku hotelu Mercure autorstwa nieżyjącego już architekta Juliusza Rouby.
Wytyczne urbanistyczne, zawarte w decyzji o warunkach zabudowy, dawały możliwość stworzenia obiektu, którego dominanta wysokościowa liczona od przyziemia do attyki osiągałaby 155 m (42 kondygnacji). Z uwagi na ograniczenia związane z sąsiedztwem, bryła została podzielona na dwie części, tzw. bazę (o wysokości do 70 m) i dominantę.
Po miesiącach analiz, w których sprawdzano ekspozycję bryły zarówno w dalekich widokach, jak i w odniesieniu do najbliższego otoczenia, przedstawiono klientowi trzy propozycje, różniące się głównie wyrazistością rozwiązań elewacyjnych. Efektem poszukiwań stała się jednolita w wyrazie forma z charakterystycznymi dynamicznymi przełamaniami płaszczyzn i homogenicznym detalem zewnętrznej „skóry”, podkreślonym kontrapunktami w postaci reprezentacyjnego holu oraz latarni – fragmentu elewacji zlokalizowanego na ośmiu najwyższych piętrach od strony północnej. Na tym etapie zdecydowano również, że większość powierzchni budynku zajmą biura pod wynajem, wyjątek stanowić będą piętra 0, +1, +14, +15, +16 oraz +39, gdzie wedle koncepcji zlokalizowane miały być funkcje reprezentacyjne obiektu. Szczególny nacisk na etapie projektu koncepcyjnego położono na uniwersalność przestrzeni biurowych, możliwość ich swobodnego aranżowania i łączenia.
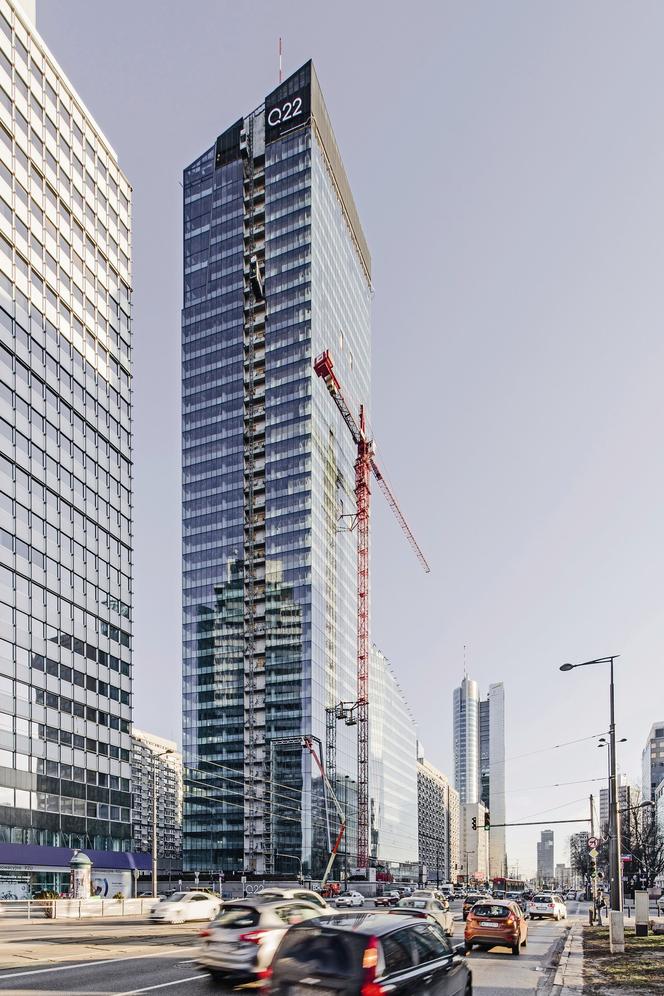
i
Komunikacja pionowa
Jednym z kluczowych zagadnień związanych z rozwiązaniami funkcjonalnymi obiektu był charakterystyczny dla wysokościowców problem komunikacji pionowej. W kontekście dość ograniczonej powierzchni rzutu poziomego typowej kondygnacji oraz podłużnego kształtu działki przeprowadzono szereg analiz uwzględniających różne typy i liczby dźwigów, jak również różne scenariusze ruchu pasażerów. W efekcie budynek został podzielony na dwie części wysokościowe i dla każdej z nich przewidziano niezależny system komunikacji pionowej. Wejścia do poszczególnych trzonów prowadzą ze wspólnego holu wejściowego. Pierwszy (6 wind) obsługuje wieżę (piętra od +15 do +39) w podziale na dwie części (Middle Rise i High Rise), drugi (4 windy) obsługuje bazę budynku (piętra od +2 do +14).
Uwzględniono możliwość dostosowania układu funkcjonalnego i konstrukcyjnego obiektu do zastosowania dwóch alternatywnych systemów wind – typu Twin (układ dwóch kabin w jednym szybie mogących poruszać się niezależnie) oraz double-decker (układ dwupoziomowych, połączonych kabin).
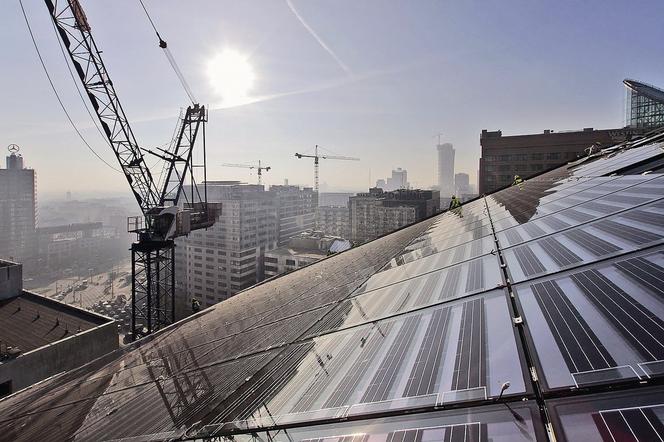
i
Decyzja o zastosowaniu zdublowanego układu kabin wymusiła na projektantach zlokalizowanie strefy komunikacyjnej holi windowych przyziemia na dwóch poziomach (parterze i pierwszym piętrze), połączonych zestawem schodów ruchomych, jak również stałą wysokość stropów. Układ ten został uzupełniony trzema dźwigami obsługującymi kondygnacje od -5 do +1, z uwzględnieniem kabin przystosowanych do transportu rowerów oraz dwoma windami pożarowo-transportowymi.
Ostatecznie, w budynku Q22 po raz pierwszy w tej części Europy zdecydowano się na zaawansowany system wind Twin, opracowany przez firmę ThyssenKrupp. Taki układ kabin, zlokalizowanych w jednym szybie jedna nad drugą, ale niepołączonych ze sobą, sprawia, że poruszają się w tym samym czasie niezależnie. Zarówno dolna, jak i górna kabina ma swój własny napęd, sterowanie i elementy bezpieczeństwa – tak jak w przypadku konwencjonalnego dźwigu. Z uwagi na optymalizację wydajności dźwigi Twin pracują wyłącznie w oparciu o system preselekcji dyspozycji (DSC). Układ ten, współpracujący z kontrolerem Twin każdorazowo wyznacza tę kabinę systemu, która w najszybszy sposób może zrealizować daną dyspozycję. Wszystkie urządzenia wchodzące w skład systemu mają funkcję oszczędzania energii, w tym m.in. odzysk energii z hamowania wind. Wnętrza kabin windowych zostały zaprojektowane przez projektantów indywidualnie. Na podstawie tej dokumentacji w fabryce ThyssenKrupp w Niemczech powstał prototyp kabiny będący podstawą dla uwag i ostatecznej akceptacji wykończeń.
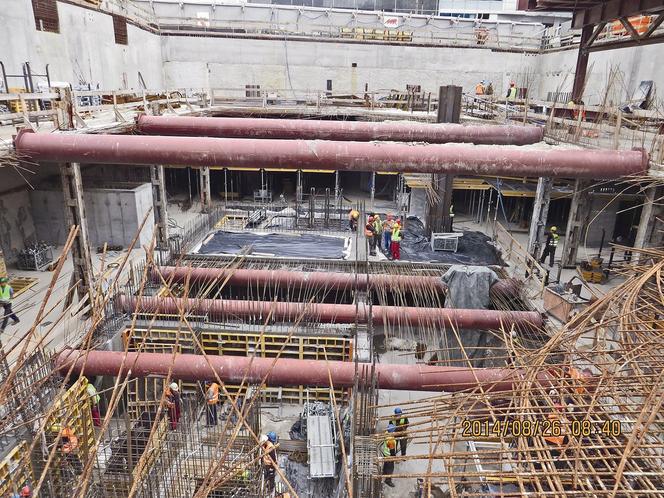
i
Elewacja
Monolityczność bryły budynku wymagała przyjęcia środków, które podkreślą jego jednolitą sylwetę, a zarazem sprawią wrażenie neutralności i dynamiki elewacji. Projekt przewidywał, że wszystkie fasady wykonane będą w systemie segmentowej ściany kurtynowej aluminiowej, a pasy międzykondygnacyjne z zewnątrz będą obłożone szkłem emaliowanym. Dla reprezentacyjnej strefy holu oraz najwyższych kondygnacji założono zastosowanie systemów fasady mocowanej punktowo o maksymalnym stopniu transparentności. Ponadto zaproponowano wewnętrzne żaluzje oraz rolety, które zapewnią ochronę przed słońcem. W trakcie realizacji przetargu na wykonanie fasady, po wielu konsultacjach z inwestorem i wykonawcą, zdecydowano o korekcie wcześniejszych założeń. Ostatecznie użyto przeziernej szyby na całej wysokości kondygnacji (3,6 m), bez podziałów i profili widocznych z zewnątrz, stosując minimalne odstępy między taflami. Długim procesem okazał się wybór szkła. Po szczegółowej analizie produktów wytwarzanych przez czołowych europejskich dostawców, porównano wizualnie kilkanaście wielkoformatowych zestawów szklanych, z których do dalszych analiz wybrano cztery. Następnym krokiem było podjęcie decyzji odnośnie metody hartowania wpływającej na charakter odbić. Finalnie zamontowano szkło SunGuard SN 70/41 oraz ClimaGuard Premium firmy Guardian, wyróżniające się bardzo wysoką przejrzystością i selektywnością, ochroną przeciwsłoneczną oraz termiczną. Zastosowane zestawy dwukomorowe charakteryzują się wartością współczynnika przenikania ciepła utrzymaną na poziomie Ug=0,5 W/(m2K) przy współczynniku przepuszczalności energii całkowitej g nie przekraczającej 0,35%.
Współpraca przy rozwiązywaniu szczegółów warsztatowych trwała kilka miesięcy. Z uwagi na kształt i stopień skomplikowania budynku wymagała od wykonawcy pracy na modelach 3d. Docelowo elewacja będzie składała się z 5000 elementów fasadowych o wadze między 300- -1100 kg każdy. Zrealizowana przez firmę DEFOR fasada będzie unikalnym rozwiązaniem segmentowym potęgującym oczekiwany przez inwestora wizualny efekt kryształu.
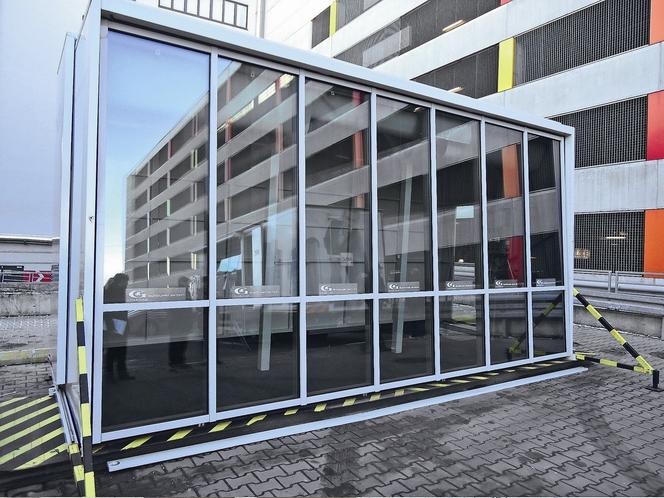
i
Fotowoltaika
Piętra od +14 do +18 zbudowane zostały w spadku elewacji 23,1°. Zgodnie z systemem BIPV zaprojektowanym przez firmę Maybatt w strukturze ściany szklanej zainstalowano moduły fotowoltaiczne light through w oparciu o ogniwa monokrystaliczne. Każdy element został stworzony jako komponent składający się z szyby ze szkła hartowanego w górnej i w dolnej części wraz z folią PVB oraz ogniwami PV i skrzynkami przyłączeniowymi zlokalizowanymi pomiędzy szybami. Moc szczytowa paneli fotowoltaicznych wynosi 76,25 kW, rocznie produkować one będą na potrzeby budynku 59,4 MWh prądu. Z uwagi na możliwość osadzania się śniegu na pochyłej elewacji, konstrukcja ogniw pozwala na ogrzanie fasady.
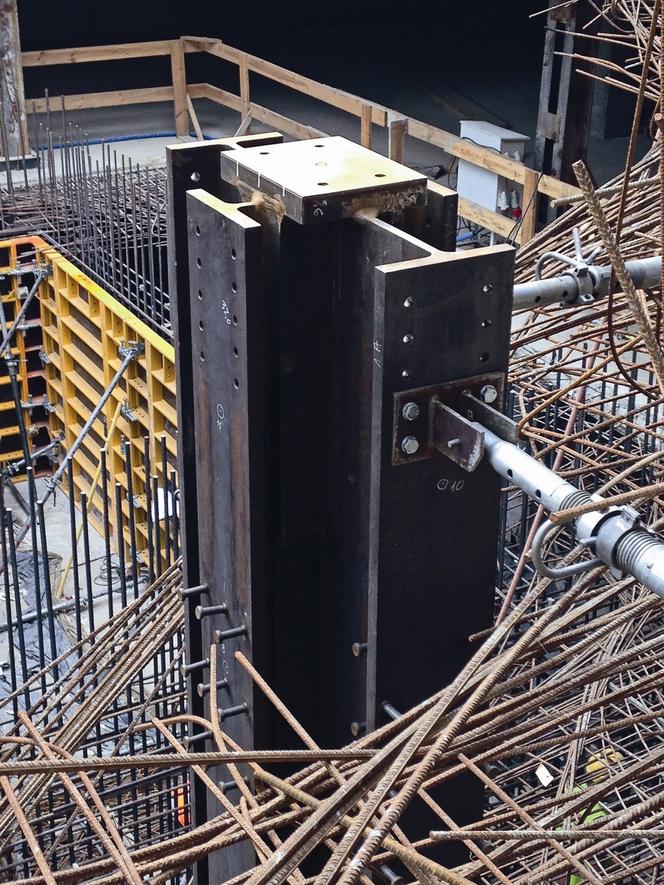
i
Konstrukcja
Uwarunkowania działki oraz wysokie wymagania architektoniczne stanowiły wyzwanie również dla projektu konstrukcji. Nietypowa bryła budynku, niesymetrycznie umieszczony trzon o szerokości zaledwie 8,4 m oraz smukłe słupy zmieniające kształt w części podziemnejto kluczowe zagadnienia, z jakimi musiał zmierzyć się zespół inżynierów. Pięciokondygnacyjne podziemie zrealizowano w obudowie złożonej ze ścian szczelinowych grubości 80 cm, których stateczność podczas głębienia wykopu zapewniono za pomocą stropów rozporowych i rozpór stalowych. Odcięcie napływu wody do wykopu uzyskano poprzez wykonanie korka w technologii iniekcji strumieniowej na głębokości około 35 m. Płyta fundamentowa (grubości od 230 do 280 cm), zaprojektowana jako fundament zespolony, współpracuje z palami i ścianami szczelinowymi. Wyzwanie stanowiła również sama bryła budynku, składająca się z dwóch części o znacząco różnych wysokościach. Elementy pionowe w obu tych częściach poddane są więc innym obciążeniom, w wyniku czego inny jest też ich skrót pionowy. Zjawisko to i jego efekty były przedmiotem szczegółowych analiz na etapie powstawania projektu. Ostatecznie zdecydowano o opóźnieniu realizacji części niższej. Wykonywanie podium rozpoczęto dopiero, gdy w części wieżowej realizowano 25 kondygnację. Dalszy przyrost obciążeń był więc podobny do przyrostu obciążeń w podium. Takie rozwiązanie stanowiło pewne utrudnienie wykonawcze. Dodatkową komplikację stwarzał fakt, że niektóre obciążenia ze słupów obwodowych wieży przekazywane miały być docelowo na trzon niższej części budynku. Konieczne było więc wykonanie tymczasowych zastrzałów sprowadzających obciążenia na trzon wieży. Zostały one usunięte po zrealizowaniu podium i podparciu słupów wieży trzonem zlokalizowanym w podium.
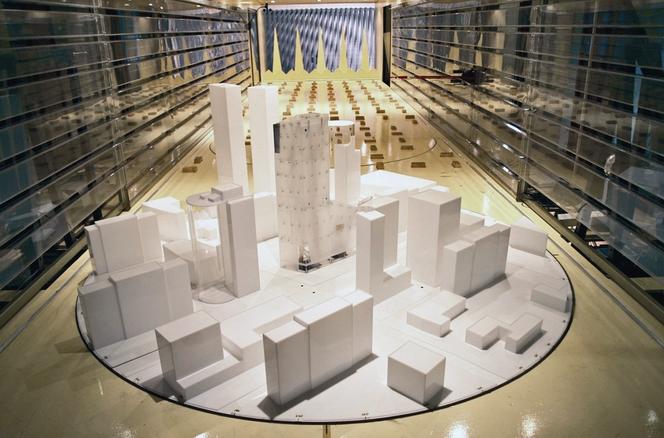
i
Innym istotnym zagadnieniem jest niesymetryczne umieszczenie trzonu w stosunku do planu piętra, podyktowane rozwiązaniami funkcjonalnymi w części podziemnej. W celu osiągnięcia zbliżonych rozpiętości przęseł płyty po obu stronach trzonu, a więc także zminimalizowania wpływu jego nierównomiernego obciążenia, od strony wschodniej wprowadzono dodatkowy rząd słupów, zlokalizowany w odległości około 4 m od trzonu budynku. Rozwiązanie takie, choć korzystne z punktu widzenia pracy płyt i trzonu, wprowadza dodatkowe elementy pionowe w bezpośrednim jego sąsiedztwie, co nie jest obojętne z uwagi na wspomniane wcześniej różnice w skrócie elementów pionowych konstrukcji. W tym przypadku z uwagi na stosunkowo niewielki przekrój poprzeczny słupów spodziewano się, że ulegną one znacznie większym skrótom od sąsiadującego trzonu. W efekcie nierównomiernemu przemieszczeniu uległyby podpory stropu.
Aby temu zapobiec, konieczne było radykalne zwiększenie sztywności tych słupów poprzez zastosowanie masywnych wkładów stalowych, wykonanych jako zespawane fragmenty grubych blach łączonych spoinami podłużnymi. Wszystkie niezbędne elementy takie jak mufy do łączenia zbrojenia stropu, łączniki grzybkowe czy połączenia nakładkowe zostały szczegółowo zaprojektowane w technologii 3d i wykonane w wytwórni. Styki czołowe kolejnych segmentów poddano frezowaniu w celu zapewnienia jak najdokładniejszego ich przylegania.
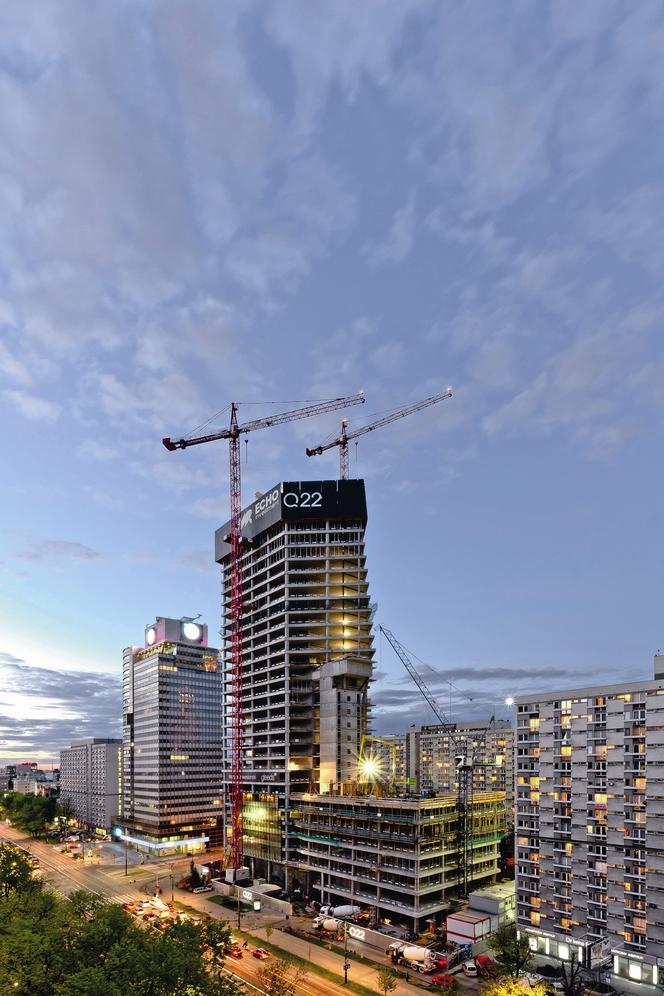
i
Wkłady stalowe wykorzystano również w części pozostałych słupów. Umożliwiło to zastosowanie mniejszych przekrojów niż w przypadku słupów zaprojektowanych jako żelbetowe. Ze względu na duże wypełnienie przekroju słupów zarówno samymi wkładami stalowymi, jak i zbrojeniem zbudowano elementy próbne w skali 1:1. Część słupów wykonano jako zbrojone prętami o średnicy 57 mm w systemie SAS670. System ten składa się z prętów o wytrzymałości wyższej od standardowego zbrojenia oraz specjalnych łączników (muf). Większy jest również asortyment dostępnych średnic zbrojenia. Zastosowanie tego rodzaju prętów pozwoliło na uzyskanie nośności słupów porównywalnych ze słupami zespolonymi. Dodatkowo przy zastosowaniu wykonywanych na zamówienie w technologii CNC szablonów opracowana została metoda prefabrykacji i łączenia dwukondygnacyjnych koszy zbrojeniowych. W efekcie znacznemu skróceniu uległ transport pionowy niezbędnych elementów i sekwencja wznoszenia słupów.
Słupy zespolone i zbrojone prętami SAS zaprojektowano również w części podziemnej. Ze względów technologicznych w kolejnych stropach rozporowych pozostawiono otwory tymczasowe, w których wykonano słupy po zakończeniu prac nad płytą fundamentową. Należy wspomnieć, że projekty konstrukcji i instalacji Buro Happold Engineering opracowało w technologii 3d, co znacznie ułatwiło koordynację międzybranżową.
Ze względu na nietypowy kształt budynku oraz występujące w bezpośrednim sąsiedztwie obiekty wysokie zdecydowano o wykonaniu badań w tunelu aerodynamicznym. Wyniki pozwoliły precyzyjnie ustalić obciążenia oddziałujące na konstrukcję i fasadę w zależności od kierunku działania wiatru.