Bałtyk
W bezpośrednim sąsiedztwie terenów Międzynarodowych Targów Poznańskich, przy rondzie Kaponiera, jednym z głównych węzłów komunikacyjnych miasta, w miejscu dawnego kina Bałtyk powstaje obiekt przełamujący konserwatywny styl nie tylko poznańskiej architektury. Nowy 65-metrowy Bałtyk o powierzchni użytkowej ok. 13 000 m2 będzie miał 16 kondygnacji nadziemnych o funkcjach biurowych i usługowych oraz 3 podziemne – gdzie zlokalizowano garaż i pomieszczenia techniczne. Autorem projektu jest holenderskie biuro MVRDV. Nasza pracownia Natkaniec Olechnicki Architekci opracowuje dokumentację techniczną, koordynuje projekt międzybranżowo oraz prowadzi nadzór budowlany.
Z uwagi na dość niekonwencjonalną bryłę, nie sposób nie wspomnieć o przestrzennych relacjach w kontekście zapisów dokumentów planistycznych. Projekt powstał w oparciu o decyzję o warunkach zabudowy. Wydawałoby się, że architekci muszą zmierzyć się tylko z ograniczeniami. Te najważniejsze to: budowa na styku z hotelem Sheraton z jednej strony i zachowanie maksymalnej wysokości zabudowy 68 m z drugiej strony działki, wymóg wygospodarowania terenu na przestrzeń miejską czy zaprojektowanie bryły, która nie zasłaniałaby całkowicie zabytkowego budynku drukarni Concordia. Projektowany obiekt należało wpisać w dość niejednorodną stylistycznie okolicę, w której dominuje jednak modernizm. Z jednej strony działki znajduje się hala targowa z charakterystyczną iglicą z końca lat 20. z drugiej – hotel Mercure z lat 60. oraz Dom Studencki Jowita UAM (również z lat 60.) na tyłach, a w środku – niewielka drukarnia z XIX wieku.
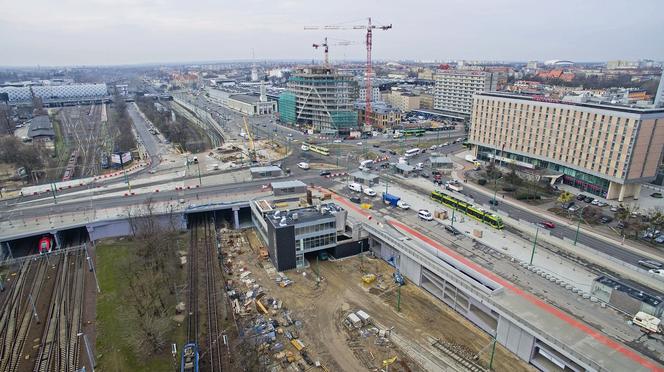
i
W związku z taką lokalizacją projekt wymagał uzyskania pozytywnej opinii Miejskiego Konserwatora Zabytków, co przy bezkompromisowym sposobie projektowania architektów z pracowni MVRDV było zadaniem niełatwym. W wywiadzie dla firmy Garvest współprojektant Anton Wubben (MVRDV) tak opowiadał o procesie projektowym: Na etapie początkowych studiów koncepcyjnych zdaliśmy sobie sprawę, że ograniczeń jest tyle, że należy zmienić perspektywę i zacząć je traktować jako argumenty „na tak”. Bryła budynku powstawała w ten sposób, że z początkowego kształtu zamkniętego granicami działki po kolei „odcinaliśmy” kolejne fragmenty. Taras południowy stanowi swoistą interpretację ograniczeń architektonicznych w tej części miasta, a olbrzymie wcięcie powstało, by zaakcentować wejście do budynku. Kolejne wcięcie zrobiliśmy, by stworzyć miejsce na taras od strony placu. Jego szerokość zachowuje równowagę między optymalizacją wielkości przestrzeni biurowej w tym miejscu a pożądanymi cechami placu. Wszystkie te wcięcia przyczyniły się więc do powstania niezwykle interesującego kształtu. Wykorzystując tę samą zasadę dla płaszczyzn poziomych i pionowych, udało nam się uzyskać fantastyczne formy, jak na przykład 7 przeszklonych kondygnacji, pnących się przed wejściem do budynku… Jestem bardzo zadowolony, że stworzyliśmy projekt, który jest odpowiedzią na wszystkie ograniczenia, a jednocześnie silnie zaznacza swoją obecność w tej wyjątkowej lokalizacji. Metamorfoza budynku w zależności od miejsca, z którego się patrzy, jest z pewnością jego wielką zaletą. Taki efekt jest zresztą logicznym skutkiem naszej interpretacji wspomnianych ograniczeń i tu właśnie, jak się okazało, drzemał największy potencjał formy, która odpowiadałaby niejednolitej w tym miejscu tkance miejskiej.
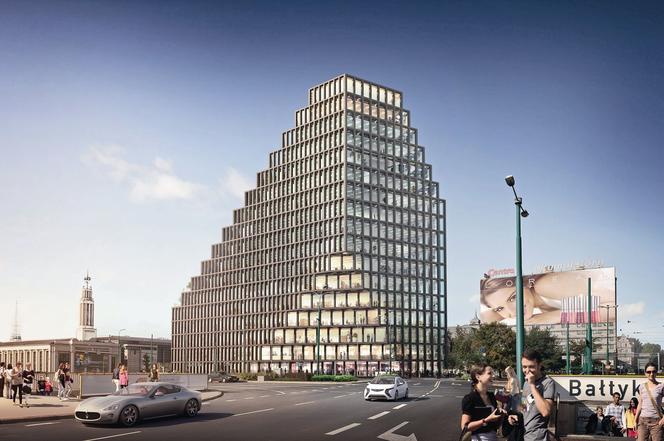
i
Konstrukcja główna
Konstrukcję budynku zaprojektowano jako żelbetową, monolityczną z elementami stalowymi. Zewnętrzne ściany podziemia (wygrodzenie wykopu) zostały wykonane techniką ścian szczelinowych o grubości 80 cm. Nad poziomem -2 założono tymczasowe, stalowe rozpory ścian, a poniżej, pomiędzy kondygnacją -2 i -3 – został wykonany otok stropu rozporowego. Bardzo lubimy charakter ścian szczelinowych, które ukazują (po ich odkopaniu) strukturę terenu w jakim zostały wykonane. Akceptujemy ich szorstkość, nie tynkujemy ich. Pozostaną bez wykończenia, tak jak żelbetowa konstrukcja w garażu, na klatkach schodowych i w przedsionkach ewakuacyjnych. Skuwanie wybrzuszeń jest konieczne tylko tam, gdzie kolidują one z instalacjami lub miejscami parkingowymi. Założeniem dla całości było uzyskanie bardzo dobrze wykonanego betonu konstrukcyjnego. Tam gdzie to było możliwe, chcieliśmy pozostawić go bez wykończenia. Dla wykonawcy, który ma bardzo napięte terminy i pracuje na trzy zmiany to dodatkowe zadanie. Akceptujemy zaproponowane podziały szalunków, ale bardzo ciężko wyegzekwować jakość betonu. Trzeba uważnie dopilnowywać m.in. odpowiedniego wibrowania i stosowania środka adhezyjnego oraz tego, aby szalunki były szczelne. A czas goni. Po ich zdjęciu okazuje się, że są miejsca, które wymagają dodatkowego działania. Wspólnie z wykonawcą omawiamy je szczegółowo i przyjmujemy program naprawczy.
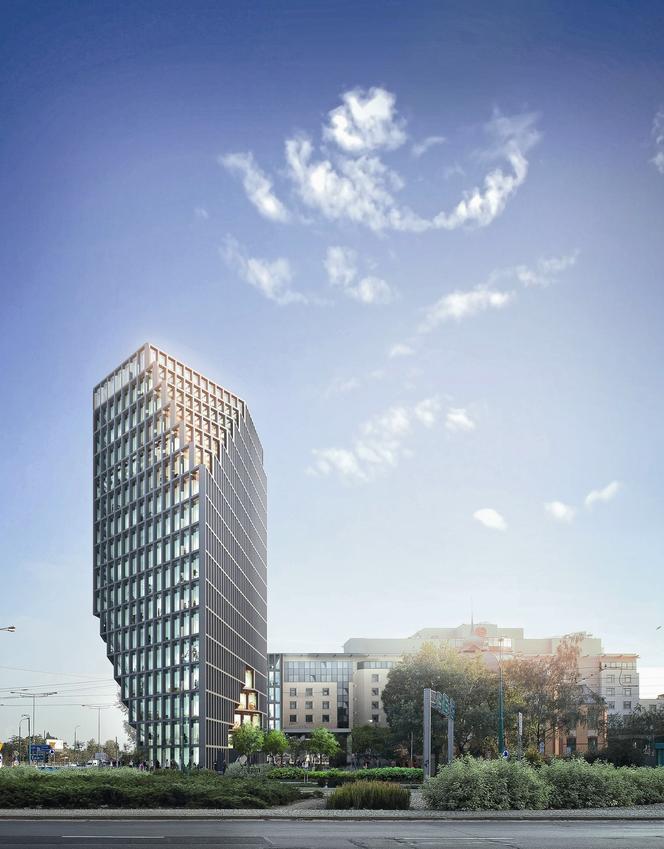
i
Najbardziej charakterystycznym elementem konstrukcyjnym są usytuowane w miejscach podcięć budynku dwie pary skośnych słupów wykonanych z betonu B60 (C50/60). Spinają one budynek i mają na celu przejęcie sił ze słupów znajdujących się na wyższych kondygnacjach. Wielkogabarytowe podpory przecinają pozostałe elementy konstrukcyjne – słupy, belki, stropy – łączą się głowicami na 5 i 7 piętrze. Ich średnica wynosi 1170 mm i zbrojone są po obwodzie 32 prętami o przekroju 40 mm. Co ciekawe, aby połączyć zbrojenia, robotnik musi wejść do wnętrza szalunku. Ze względu na nietypowe formy węzłów zaprojektowano również indywidualne szalunki. Słupy miały zostać niewykończone – betonowe. Okazało się jednak, że z uwagi na ich skośne ułożenie, w górnych partiach są problemy z odpowietrzeniem szalunków. Powierzchnie nie są tak idealne jak oczekiwaliśmy, więc zdecydowaliśmy, aby je zaszpachlować i pomalować.
Trzon, który jest spinającym i stabilizującym korpusem budynku w początkowej fazie projektu, z uwagi na jego „podcięcie” na dolnych kondygnacjach, nie zapewniał odpowiedniej stateczności – rozciągane na górnych piętrach (od strony placu) żelbetowe słupy spowodowały, że budynek zaczął się lekko przechylać. Ostatecznie założono, że poziome wychylenie trzonu nie może przekraczać wartości H/500, gdzie wysokość H wynosi 65,2 m. Długo trwała praca nad koordynacją otworów w trzonie. Szło naprawdę o centymetry. Z jednej strony projektanci konstrukcji, z drugiej projektanci instalacji i my jako koordynatorzy pośrodku. Skończyło się na 4,59 cm – to wartość maksymalnego wychylenia budynku na najwyższej kondygnacji.
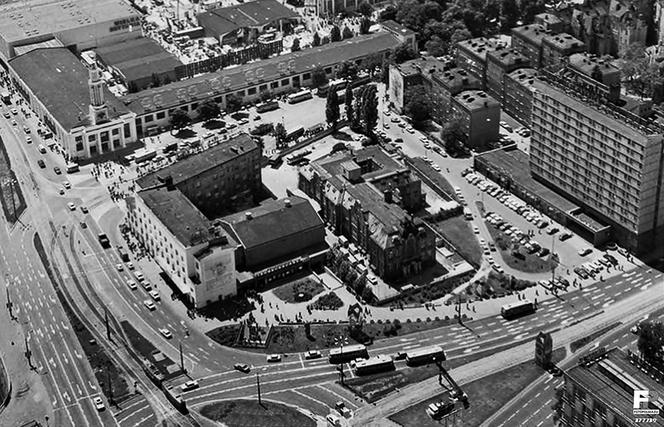
i
Szklane stropy (podłogi)
Jednym z najbardziej nietypowych rozwiązań zastosowanym w projekcie są szklane stropy w miejscach podcięć. W projekcie zakładano również wykorzystanie szklanych zadaszeń nad schodkowo uskakującą bryłą od strony południowej. Niestety, ze względu na olbrzymie zyski ciepła nie udało się tych elementów zachować.
Stropy zbudowane są z dwóch warstw szklanych paneli. Panel dolny, o grubości 30 mm, stanowi warstwę ogniochronną, natomiast panel górny, ze szkła laminowanego, o łącznej grubości 41 mm, spełnia funkcję pomostu. Konstrukcję wsporczą dla elementów szklanych stanowi ruszt z profili stalowych. Jego belki spawane są ze sobą w taki sposób, aby zapewnić płaszczyznowość górnej krawędzi oparcia paneli. Ich układ odpowiada kształtowi i położeniu szklanych elementów, tak aby wszystkie krawędzie opierały się na górnych półkach belek. Uszczelnienie połączeń pomiędzy panelami oraz panelami a konstrukcją wsporczą zapewnia system uszczelek. Całość na budynku mocowana jest do stalowej konstrukcji składającej się z konsoli stropowych i wieszaków z belek dwuteowych.
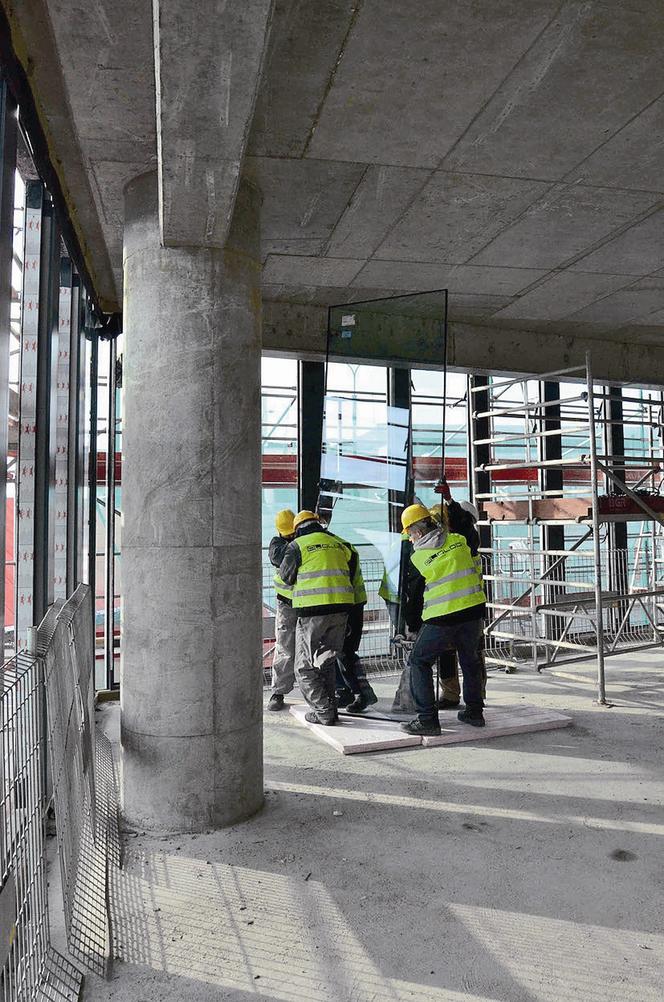
i
Fasada
Założenia dotyczące fasady na początku były dość ogólne – „betonowe elementy”, „trochę szorstkie”. Mieliśmy też próbkę materiału wzorcowego dostarczoną nam przez MVRDV. Rozpisany został przetarg, a my pozostaliśmy z pytaniami: kto ma wykonać 11 km prefabrykowanych belek i słupów bez możliwości składowania ich na placu budowy? Jak rozwiązać kwestie ich transportu? Kto ma odpowiednie referencje, zaplecze techniczno-inżynierskie, bazę produkcyjną? Zaczęliśmy jeździć i sprawdzać potencjalnych producentów. Odwiedzaliśmy zakłady m.in. we Wrocławiu, Krakowie, Poznaniu, Brnie, pod Monachium i w okolicach Antwerpii. Część firm miała duże doświadczenie, niektórzy dopiero zaczynali. Na dodatek zaczęliśmy się wspólnie z generalnym wykonawcą zastanawiać, jaką wybrać technologię w kontekście rozwiązań technicznych jak i estetyki. Jaki będzie miała wpływ na kwestie pożarowe, a także poprzez ciężar elementów na obciążenie krawędzi stropów? Jak będzie wyglądała podkonstrukcja i system regulacji elementów wieszanych? Każdy proponował nam inne rozwiązanie. Kwestie finansowe nie były bez znaczenia, ale wszyscy zdawali sobie sprawę, że w tym przypadku nie możemy oszczędzać. Na budowę przywożono kolejne próbne elementy, a my staraliśmy się je właściwie ocenić, wyłapać mocniejsze i słabsze strony. Przedstawiane propozycje nas jednak nie urzekały, a wiedzieliśmy że materiał, z którego wykonana jest fasada musi mieć to coś – ma migotać w słońcu.
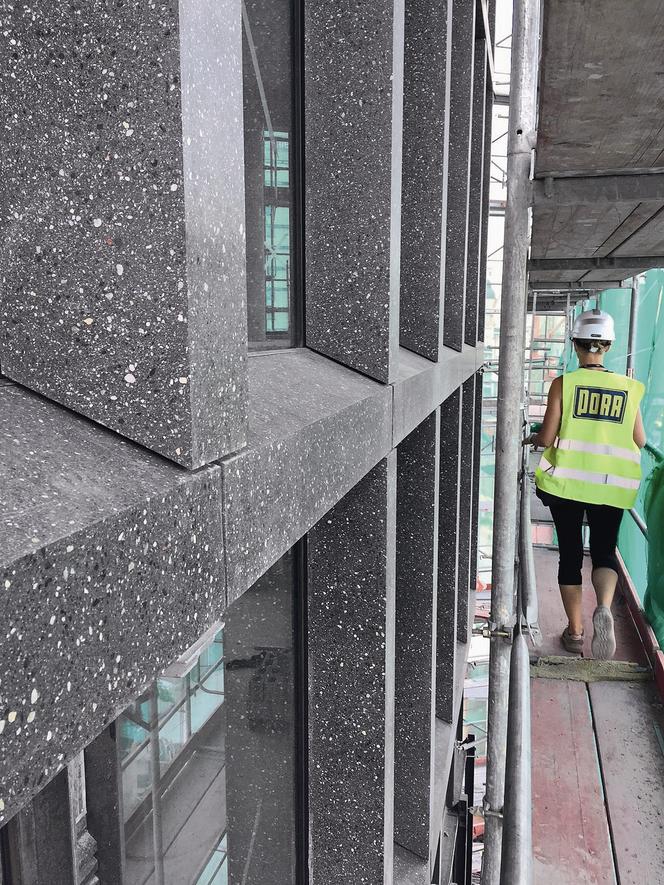
i
Samo dosypywanie miki nie dawało tych rezultatów. Kluczem okazało się, poza odpowiednio dobraną mieszanką betonu, szlifowanie. Ukazywało jego wewnętrzną strukturę i sprawiło, że zaczynał wyglądać jak „materiał za milion dolarów”. Dodatkowo wyostrzało pionowe krawędzie, dając elementom precyzyjny sznyt. Wspólnie z MVRDV ustaliliśmy docelowy skład mieszanki, dobierając proporcje odpowiednich kruszyw.
Ostatecznie okładziny elewacyjne zostały zaprojektowane i wykonane w postaci grubych na 25 mm prefabrykatów GRC z betonu zbrojonego, włóknami szklanymi rozproszonymi w masie. Słupy fasadowe mają wysokość 360 cm, natomiast długość belek waha się w granicach 135-405 cm. Elementy te wykonywane są na płasko, na łamanych szalunkach. Aby uzyskać monolityczny kształt przestrzennego prefabrykatu, po wstępnym związaniu mieszanki składa się go na specjalnych zawiasach. Dla każdego typu wykonywane są dokładne obliczenia przez wykonawcę i projektanta fasady. Elementy poziome zostają dodatkowo wzmocnione w wewnętrznych narożach.
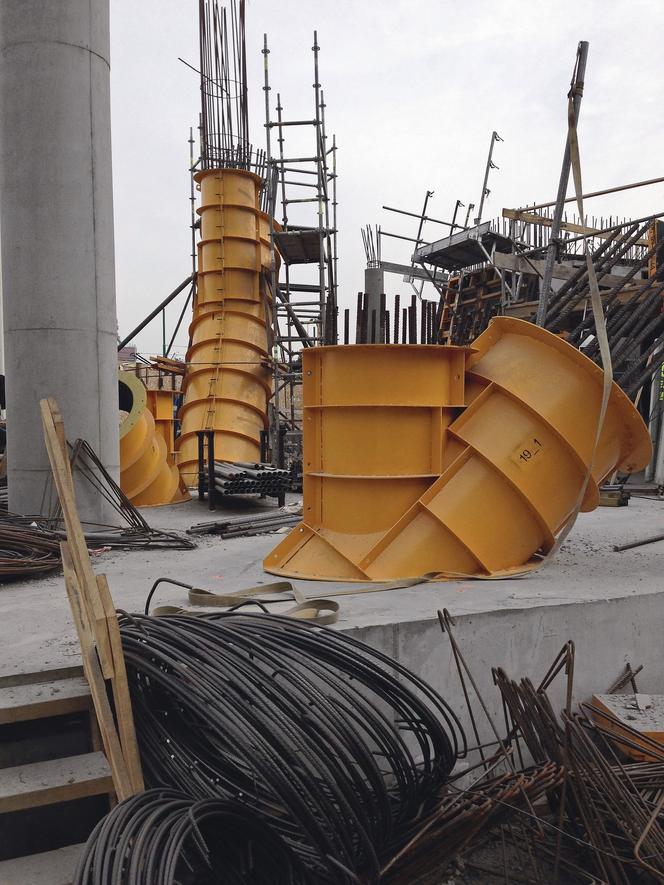
i
Mimo to muszą być transportowane na górę przy użyciu specjalnego trawersu, aby obciążenia inne niż docelowe nie spowodowały uszkodzeń. Prefabrykaty mocowane są do konstrukcji kotwami tyłowkrętnymi poprzez układ kątowników przytwierdzanych z kolei do stalowej konsoli ocynkowanej ogniowo. Przyjęty sposób wykonania sprawdza się przy podstawowych typach elementów. Jednak złożony kształt budynku i rygorystyczny rytm elementów pionowych generuje wiele nietypowych detali w narożach. Ich kształt jest bardziej skomplikowany niż podstawowy typ C i niemożliwy do wykonania w jednej części. Aby uzyskać efekt monolitu, elementy łączone są mechanicznie w niewidoczny sposób.Przed przystąpieniem do wieszania modułów uzyskano odpowiednią opinię wraz z pozytywnym wynikiem badania w zakresie odpadania elementów elewacji w przypadku pożaru. Zbudowano model testowy i poddano go próbie ogniowej. Podczas montażu największe trudności sprawia dopasowanie poszczególnych elementów, zachowywanie odpowiednich szczelin dylatacyjnych oraz pionowanie i poziomowanie. Tolerancje wykonawcze i możliwe odchylenia w produkcji powodują konieczność ręcznego doszlifowywania. Zajmuje to oczywiście dodatkowy czas i wymaga precyzji wykonania, czasami kilkukrotnego zdejmowania i wieszania tego samego elementu. Zakończenie realizacji planowane jest na I kwartał 2017 roku.
- Autorzy: MVRDV
- Konstrukcja: Akon
- Inwestor: Garvest Real Estate
- Nazwa obiektu: Biurowiec Bałtyk w Poznaniu
- Generalny wykonawca: PORR
- Współpraca: Natkaniec Olechnicki Architekci
- Elewacje: Biuro Techniczne Tuscher
- Instalacje sanitarne: Termo Studio
- Instalacje elektryczne: Janura
- Planowane zakończenie realizacji: 2017